Increasing Distillate Production at Zero Capital Cost
Significantly increasing distillate production can at the earliest stages require no more than process tweaks before significant capital revamps are required
JOE MUSUMECI, STEVEN W STUPIN, STEPHANIE SCHLOSSER and THOMAS SCHOLTEN
Ascent Engineering
This is the first of two articles which discuss changes to the crude unit to help produce a higher percentage of distillate products from each barrel of crude processed. The discussion begins with a review of operational tweaks and changes that require zero capital investment. A second article for PTQ will discuss additional opportunities that exist for increased distillate yield, considering options that require minimal capital investment as well as major capital projects that can increase distillate yield.
Within the crude unit, optimisation of existing equipment for maximum distillate yield can bring increased profits with no capital investment and low technical risk. Because the modifications covered here are operational only, there is no need for additional equipment and the operational changes can be reversed if need be. Plant data and a simulation model of the unit combined with a thorough review of the existing equipment allow a refiner to highlight areas within the crude unit with the greatest opportunity to impact distillate recovery.
Diesel Demand Continues to Rise
Most US refineries have been designed and operated to maximise gasoline production since the early 1940s in order to meet the demand from the mass produced, gasoline powered vehicles that dominated the consumer market. In addition, the advent of higher compression gasoline engines required additional refinery processing to keep up with gasoline quality and yield demands. However, current shifts in worldwide fuel consumption patterns are affecting demand for gasoline and diesel. Factors that contribute to the shift in consumption patterns include increased demand in developing countries, a focus on reducing greenhouse gas emissions that has led to more stringent automotive fuel efficiency standards, and increased blending of renewable fuels.
Future demand for diesel fuel is projected to continue to grow while refined gasoline demand is projected to continue to decline and this trend is projected to continue through 2040, as can be seen from the Annual Energy Outlook projections for the United States from the Energy Information Administration of the US Department of Energy (see Figure 1).
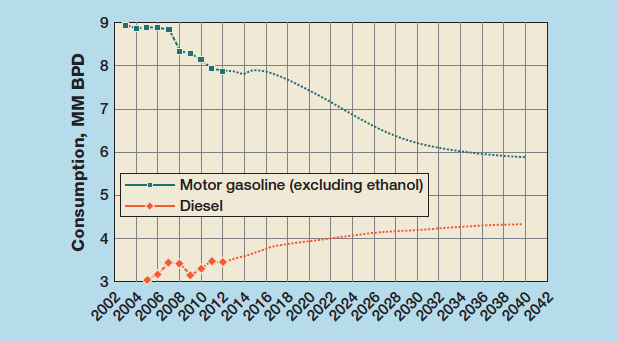
Figure 1 United States gasoline and diesel consumption
US total diesel fuel consumption is projected to increase from current demand of about 3.5 million b/d to 4.3 million b/d in 2040. Future US diesel exports are also projected to grow to meet the demands of emerging international markets. Exports of ultra-low sulphur diesel (ULSD) to Europe are on track to almost double in the first half of 2014 compared to 2013 as US refineries continue to benefit from cheap crude prices. Distillate fuel exports to Central and South America, the largest destination for US produced distillate fuel, increased by 12% in 2013. In addition, Latin America is importing more distillates as a result of tightening fuel regulations and limited refining capacity at existing refineries.
US consumption of finished motor gasoline is projected to decline by approximately 2.1 million b/d over the next 25 years as consumers transition to more fuel efficient and alternate energy vehicles. This is largely as a result of the Corporate Average Fuel Economy (CAFE) and Greenhouse Gas (GHG) emissions standards set by the National Highway Traffic Safety Administration (NHTSA) and the Environmental Protection Agency (EPA). Also, the US has been a net exporter of finished motor gasoline, with average annual export volumes increasing from 0.07 million b/d in 2010 to roughly 0.44 million b/d to date.
Vehicle miles travelled (VMT) are projected to increase diesel fuel consumption by approximately 0.9 million b/d from 2012 to 2040, despite increases in renewable fuel blend volumes resulting from the Renewable Fuel Standard (RFS) programme. The RFS was established by the Energy Policy Act of 2005 and expanded by the Energy Independence and Security Act of 2007 (EISA2007). The RFS requires the EPA to set annual percentage standards for the renewable content of gasoline and diesel fuel. Refiners and importers of gasoline and diesel fuel are then obligated to blend renewable fuels in proportion to the volumes of non-renewable gasoline and diesel fuel sold. The proposed 2014 total blending requirement is 15.2 billion gallons of ethanol equivalent renewable fuel, with the mandate reaching 36 billion gallons by 2022.
The price differential between diesel and gasoline is driving the change at refinery level to target more diesel production. Since 2004, diesel prices have typically exceeded that of gasoline in US markets (see Figure 2). This is a reversal of the typical historical price relationship for diesel and gasoline and is driven by supply and demand for the two fuels.
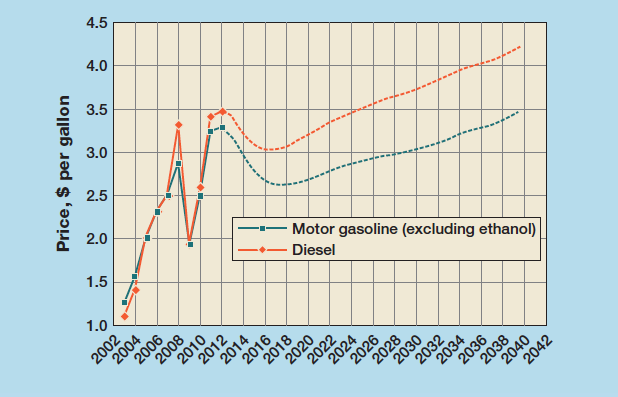
Figure 2 US gasoline and diesel prices
It is projected that these worldwide consumption patterns will continue in response to increased demand in developing countries, comtighter fuel efficiency and emissions standards, and rising RFS programme mandates. The US diesel to gasoline price spread is projected to grow to $0.75/gal by 2035 (see Figure 3). Also, as a result of new crude sources and fracking technologies, the US is expected to continue to be a net exporter of petroleum products. Although the nation will still consume gasoline as its primary transport fuel for the foreseeable future, refineries have begun to react to market conditions and will continue to increase middle distillate production. This trend will impact refinery operations and investment. Refiners who can adjust to these and future market conditions and produce higher yields of the most valuable distillate products will maximise refinery profitability.
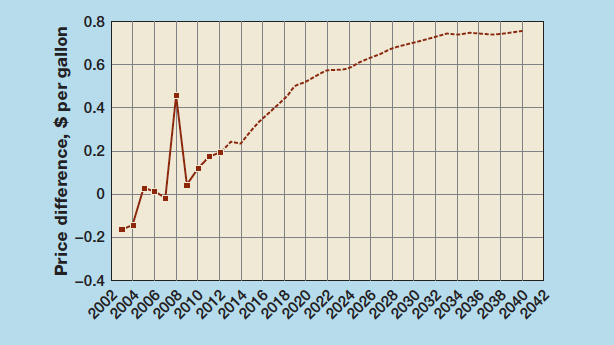
Figure 3 US diesel to gasoline price differential
Yet, because of uncertainties in the markets and slow economic recovery, many refiners have not allocated resources for major capital projects. Those refineries which are capital constrained should re-evaluate their gasoline and distillate products strategy to take advantage of many potential zero capital cost opportunities to maximise distillate yield with an eye to low cost projects for increased distillate yield.
Producing a base case simulation model matched to valid, mass balanced plant data should be the first step in the crude unit’s evaluation. The model’s accuracy should be checked against plant, lab and operating data, as well as known operating limits. From this simulation, optimisation cases can be analysed to increase distillate production and to help to identify bottlenecks and operational opportunities that can have excellent payout often with little or no capital investment. Also, economic evaluations can be made to help determine future capital projects. Key to identifying these opportunities is modelling and design experience as well as operational guidance, the responsibility for which usually falls on the shoulders of the often overwhelmed refinery process engineering staff. The authors have worked closely with staff at multiple refineries to perform these types of evaluations with results that have successfully increased profitability.
Optimise Current Operations: the Zero Capital Investment
For most refineries, improving diesel recovery through operational modifications means starting with an examination of the operation of the atmospheric tower and its side strippers. Improved diesel recovery from the atmospheric tower requires improved separation of the diesel range material from the lighter and heavier fractions in the tower. In most typical units, a significant amount of diesel range material ends up in the atmospheric tower bottoms due to the vapour liquid equilibrium of the flash zone. The amount of diesel range material lost to the atmospheric bottoms is greater for heavy crudes due to the larger amount of lower vapour pressure, heavier components. The following discussion highlights operating variables that can be adjusted to improve diesel recovery.
Atmospheric Tower: Optimise Stripping Steam
Crude unit stripping steam is often given inadequate attention. In many refineries it is not uncommon for the atmospheric tower stripping steam to be poorly monitored and not optimised. Yet stripping steam rates have a large effect on diesel recovery. Adequate stripping steam is especially important with heavy crude slates, since stripping steam reduces hydrocarbon partial pressure, thereby increasing light hydrocarbon vaporisation without increasing temperature. This allows higher light product recovery from heavier crude fractions. In the stripping section of the atmospheric tower and the AGO side stripper, increased stripping steam directly increases the amount of diesel recovered.
Typical limitations to the increased use of stripping steam are column flooding, the inability to remove energy from the atmospheric tower either through limits in the pumparound heat exchangers or in the overhead condensing system, and operating too close to water dew point which can cause additional corrosion and potential plugging. Simulation of the operation of the atmospheric tower, including its side strippers and pumparounds and other auxiliary equipment, is beneficial for finding the optimum rate of stripping steam to achieve the maximum recovery of diesel, within the limits of the existing equipment.
In one medium-sized US refinery, we helped the engineering staff increase diesel yield by 3% of crude as a result of increasing stripping steam to the atmospheric tower. As part of a project scope to improve operation of the refiner’s vacuum tower, it was noticed that a significant amount of diesel range material was leaving the atmospheric tower in the bottoms stream. The plant was unable to increase stripping steam rates because of tower flooding. Ascent simulated the crude tower and determined that, by increasing the stripping section steam rate and slightly increasing the tower operating pressure, we could significantly improve diesel yield and still avoid tower flooding. Increasing tower pressure typically hurts diesel recovery, but our simulation proved that the increase in stripping steam more than compensated. Figure 4 shows the atmospheric tower configuration.
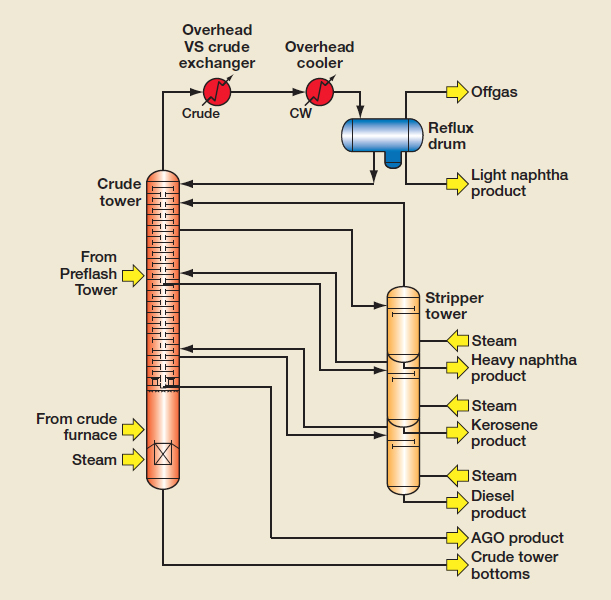
Figure 4 Atmospheric Tower Configuration
Based on our recommendation, the refinery performed a test run of various stripping steam rates in the atmospheric tower. Figure 5 shows the observed results based on plant data for several different stripping steam rates. The diesel yield as a percent of crude charge increased from approximately 21.5 LV% to 24.5 LV% by increasing the atmospheric tower stripping steam rate from 3.6 to 6.4 lb/bbl. In order to achieve these stripping steam rates, the tower operating pressure had to be increased slightly to avoid flooding from the extra stripping steam and additional vapour traffic. Simulation work suggested that a 5 psi increase in tower operating pressure would maintain constant tray flooding while the stripping steam rate was increased. Plant data show that the actual tower pressure was increased by approximately 3 psi.
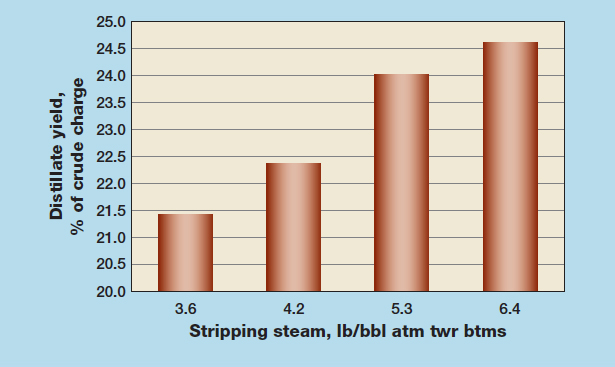
Figure 5 Atmospheric Tower Stripping Section Steam Rate
At this refinery, this simple operational adjustment increased diesel yield by 3% of crude. At current prices, assuming a $0.23/gallon price incentive for diesel over gasoline as per Figure 3 above, the additional profits that result from these modifications can approach $5.7 million/y with no capital investment. Assuming the price projections are correct, the profit incentive increases over time as the price difference between diesel and gasoline increases.
Stripping Steam in Side Strippers
Stripping steam is used to meet flash point specifications and improve fractionation in the product side strippers. Side stripper optimisation can be complex and should be verified with accurate simulation modelling. To increase total distillate yield, the diesel stripping steam flow rate may need to be reduced to meet the minimum product flash point specification. The refiner should consider minimising limits to the flash point based on constraints such as pipeline, transportation or other safety concerns. The amount of stripping steam that is reduced from the diesel stripper can be injected into the atmospheric tower stripping section or AGO stripper, which will further improve diesel recovery. Stripping steam to the kerosene stripper should be maximised up to a condenser, flooding, water dew point limit or other limit which will increase fractionation between the naphtha and kerosene cuts, thereby allowing the refiner to undercut more barrels of naphtha into the kerosene product and minimise the naphtha 90% point while maintaining flash specification on the kerosene product.
Atmospheric Tower Pressure
A reduction in atmospheric tower operating pressure will result in increased distillate recovery. This is because reducing tower pressure reduces hydrocarbon partial pressure directly and increases distillate recovery because more of the lighter material stays in the vapour phase and travels up the tower. Reducing the tower operating pressure is typically subject to the limits of the overhead condenser, since lower pressure corresponds to a lower condensing temperature and, thus, less log mean temperature difference (LMTD) available for the condenser to achieve adequate cooling. The tower itself must also be examined, as lower operating pressure will increase volumetric comvapour rate and will increase tower flood. It is important to keep in mind, as in the previous stripping steam discussion, that the refiner may find that increasing the tower operating pressure while increasing stripping steam or heat input yields greater benefit. Accurate simulation matching operation is a powerful tool for optimisation of the atmospheric tower’s pressure profile.
Atmospheric Tower Overflash Rate
Optimising the wash oil rate can minimise diesel and AGO losses from the atmospheric tower. Wash oil, typically AGO with some diesel range material, is fed to the wash bed to reduce entrainment in the flash zone. Wash oil leaving the bottom of the wash bed is called overflash and it can drag diesel and AGO product with it. Reducing the wash oil rate can minimise diesel and AGO losses, but it can be at the expense of drying out the wash section trays or packing which can cause fouling by coke formation. The optimisation goal is to minimise the atmospheric tower wash oil rate while keeping adequate liquid to prevent coke formation and maximise product rates.
When considering wash oil rate changes, because of the coking risk, it is important to complete a review of the tower’s operating history and to have an accurate measurement of the wash oil rate verified by a stable simulation of the tower. The simulation can be used to verify overflash and quantify expected recovery gains. There are several modelling techniques discussed by others that can be used to accurately model the tower flash zone and to calculate wash oil rate and to ensure adequate liquid is supplied. Also, other means may be available to help improve the accuracy of the model. These include both direct measurement of flow and estimation of flow based on measurement of other variables such as differential temperature across the wash trays or bed, slop wax temperature, and sump temperature.
Coking is not the only consideration when adjusting the atmospheric tower’s wash oil rate. Care must be taken to evaluate the impact that changing the wash oil rate has on the AGO and diesel quality and product specifications. If the diesel becomes black, for example, it can be assumed that there is insufficient washing in the bed, and the overflash rate should be increased.
Atmospheric Tower Pumparound Rates
Increasing tower pumparound duty generally increases the energy transferred to cold crude charge. For an atmospheric tower heater that may be at its limit, this increased duty will correspond to increased heater inlet and outlet temperatures and will increase lift without additional burden on the heater. This may result in increased internal reflux below the pumparound if the tower charge temperature is increased, which can sharpen fractionation in this section. Above the pumparound, however, internal tower reflux can be decreased if pumparound rates are increased too much, which may decrease fractionation and in the worst cases cause tray dry out. Care must be taken to optimise pumparound duty and associated diesel lift while minimising the negative effect on product fractionation in order to maximise the distillate draws. Careful unit review and simulation can optimise the competing effects and result in significant economic incentives.
Simulation is a powerful tool to optimise the complex interactions of the pumparounds, increased energy recovery from the preheat train, and increased atmospheric heater inlet and outlet temperature. Simulation, operating, and process knowledge can be used to optimise heat recovery with a full review of the exchanger train including operating limits on the desalter, product cooling, and heater limits. Additionally, a heat exchanger train review can help identify overly fouled exchangers, high pressure drops, design pressure limits, high exchanger tube velocities, and potential exchanger tube vibration problems.
Sometimes small changes in pumparound rates can improve product yields and can greatly improve profitability. In one case, we recommended adjustments to crude tower pumparound rates to reduce the AGO pumparound (Figure 6), while increasing in the diesel pumparound and maintaining the crude charge temperature. The expected benefit of this recommendation was to allow diesel range material that might be condensed in the AGO pumparound section to stay in the vapour phase and move up the tower to the diesel section, where it would be condensed and drawn off as diesel. The higher diesel pumparound improved the internal reflux rate between the diesel and AGO draws, which sharpened fractionation between the two products. Sharper fractionation may also improve diesel cloud point, which allows for a deeper diesel cut and further increases in the diesel draw rate. The operational change was confirmed by simulation and it was determined that the shift from AGO to diesel should yield approximately 0.3 LV% additional diesel on crude charge.
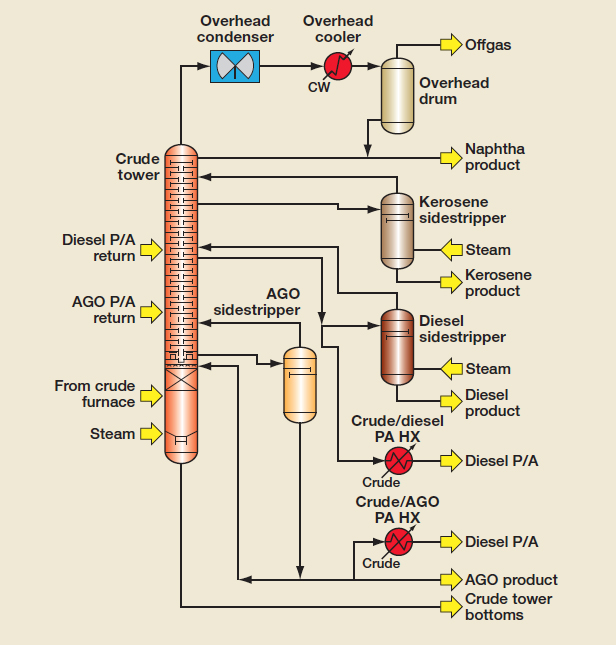
Figure 6 Atmospheric Tower Configuration
Diesel not properly recovered from the AGO will be directed to downstream processing units, taking up unit capacity, increasing costs to recover and quite likely cracked, reducing overall distillate yield. This relatively common practice can be improved. If AGO feeds a FCC unit, diesel range material that is not recovered upstream consumes capacity, cracks to lighter materials, and increases light cycle oil (LCO) production. It has been shown by others that 8% straight run diesel in a FCC unit’s gas oil feed will result in a loss of 5.5% total distillate range material (straight run diesel + LCO) and may have lower cetane quality.
In the case above, the client confirmed expected diesel rate improvements with the lower AGO pumparound flow rate. Data were collected during a period in which the crude slate, charge rate, and product specifications were held constant, and only the AGO pumparound rate changed. The test results are shown in Figures 7 and 8. Figure 7 shows that there is an inverse relationship between AGO pumparound rate and distillate yield. Reducing the AGO pumparound rate resulted in an increase in distillate yield. When the AGO pumparound rate was later increased, the distillate yield dropped. Figure 8 shows that reduced AGO pumparound rate resulted in reduced AGO yield. The two figures together indicate that diesel range material moved from AGO to diesel product when the AGO pumparound rate was reduced. During this test it was confirmed that kerosene flash and initial points remained constant and the diesel D86 90% did not change significantly, indicating that increase came as a result of improved fractionation. The middle distillate yield increased during this period from 34.2% to 34.7%, or approximately 165 b/d. For this refiner, a $20/bbl diesel to gas oil incentive was used, which amounted to potentially $1.1 million/y additional profit with no capital investment. The results in your refinery can be predicted with accurate data matching and modelling.

Figure 7 Diesel Yield vs AGO Pumparound
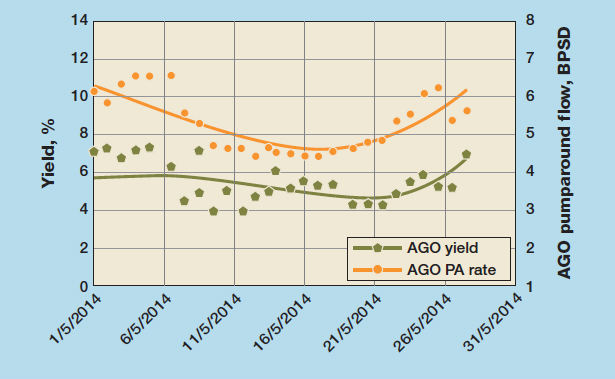
Figure 8 AGO Yield Versus AGO Pumparound
Atmospheric Tower Overhead System
Optimisation of the atmospheric tower overhead system can have a significant impact on distillate yield and on crude unit performance as a whole. Changes to reflux rate or reflux temperature can affect fractionation and distribution of the side cuts – for example, a lower overhead temperature may be used to maximise the amount of naphtha dropped into kerosene. Generally, cooler or increased reflux will sharpen fractionation, whereas warmer or decreased reflux will reduce fractionation. Changes in the overhead temperature profile, however, may have other consequences. Operating the tower overhead at too low a temperature may cause increased corrosion and plugging due to salt formation, causing unplanned shutdowns and more frequent equipment maintenance. A balance must be struck between finding the optimal reflux rate to maximise distillate recovery while avoiding operating too close to water dew point.
A review to minimise the corrosion issues in the overhead system should begin at the desalter. As part of any crude unit review, the desalter history should be examined for proper operation, including looking for plugging in the level taps, proper control of desalting chemicals, quality of the desalter water, and properly functioning electrical grids. Salts not removed in the desalter will end up in the tower’s overhead system.
Low crude overhead temperatures that operate too close to water or salt dew point will cause corrosion and fouling on the top tower trays. The dew point temperature will increase with increased stripping steam rates and crude water content. The overhead water dew point should be checked to ensure operation with sufficient margin to minimise risk free water formation, salt plugging, and corrosion on distillation trays.
In addition, the wash water system should be examined for proper operation, including correctly installed filters, water quality, and control of wash water flow rate. The wash water rates should also be checked to verify that there is enough free water after the wash injection point(s) to prevent high salt concentration, corrosion, and plugging issues in the overhead condensers and downstream equipment.
Atmospheric Heater
Increasing the crude feed preheat and optimising the atmospheric heater operation is another way to increase diesel recovery from the atmospheric tower feed. Heaters are often operated at or above their design limits. Any way that the refiner can increase the heater outlet temperature, or unburden the heater by achieving increased inlet while maintaining or increasing the outlet temperature, can have a significant impact on unit operations. In general, the atmospheric heater outlet temperature should be maximised and is usually limited by the capacity of the preheat train, pumparound and condenser exchangers, fuel quality, preflash tower, atmospheric heater, and heat transfer line and inlet horn. Achieving the maximum temperature within equipment limits allows maximum diesel lift from the atmospheric tower feed.
Heater optimisation begins with proper heater operation, including regular maintenance and on design operation. Clean burner tips, properly functioning air registers, soot blowers, flue dampers, and a properly located and functioning oxygen analyser all affect the ability to achieve the maximum heater outlet temperature. Operating with a fuel quality that allows the maximum duty from the installed burners and consistency of fuel quality are important to achieving the maximum diesel lift from the atmospheric tower feed.
Maximising the atmospheric heater outlet temperature can help maximise diesel recovery. Typically, heater outlet temperatures should be in the range 680-710°F (360-375°C) and can be higher based on crude slate and heater design. Potential limits on heater operation may be temperature limits based on tube wall thickness and metallurgy, thermal coking and crude stability, environmental and permit limits, and so on. The evaluation should also consider maximum tube wall temperature, maximum flux rate, and residence time.
If the crude unit has an existing preflash tower, increasing the inlet temperature to the preflash tower can unload the atmospheric tower heater as well as unload the naphtha section of the atmospheric tower. The heater duty may then be increased for additional crude charge or for higher heater outlet temperature at the existing charge rate. Increasing crude charge produces more diesel by processing more material while increasing the atmospheric heater outlet temperature may allow for greater diesel recovery. Increasing crude charge may require some level of equipment review to ensure design pressures are not exceeded during an upset.
Crude Slate
Although crude slate selection is beyond the control of a typical unit engineer, it can provide an opportunity for increased diesel recovery. By selecting a crude blend that best matches the refinery’s equipment capabilities, product yields can be maximised. A simulation model can be used with a crude assay data to predict the diesel recovery on crude for the atmospheric tower. For valid results, the simulation will require an accurate representation of the blended crudes. Crude assays should include high temperature simulated distillations (HTSD) and light ends analysis detailing the relative amounts of compounds through nC5 as a minimum, and preferably through nC6. This information is required to model properly the crude unit’s operation and to predict accurately operation of the heat exchanger train, preflash, and atmospheric and vacuum towers.
Other considerations to crude blending are crude compatibility, salt and organic acids, sulphur, nitrogen, solids and metals, and so on. For example, perhaps a refiner is considering introducing light, tight oil into the crude blend to help unload vacuum tower capacity and produce more distillate products. A big concern is crude compatibility when the refiner plans to blend tight oil crudes, which are highly paraffinic, with heavier asphaltenic crudes. Specifically, the mix of paraffinic and asphaltenic crudes can cause destabilisation of the asphaltene, which in turn allows the asphaltenes to agglomerate, crack, precipitate and eventually form coke-like deposits in pipes and equipment. Beyond the crude unit, metal contaminants such as silicon, iron, calcium and heavy metals can have a significant impact on downstream catalyst units such as the FCC unit, hydrotreaters and hydrocrackers.
With good assay data and a good simulation, however, the refiner can identify opportunistic crude blends that have properties and a product distribution that are a good match to the existing equipment limits. Identifying the crude that is a best match to the existing equipment can allow the refiner to maximise profitability.
Conclusion
As demand for diesel is projected to exceed demand for gasoline in the years to come, refiners are wise to consider how they can adjust to these market conditions and increase profitability by maximising production of the most valuable products. Finding resources for major capital investment may be difficult, but there are a number of zero capital cost investments that a refiner may consider for the crude unit operation that can increase distillate production and improve profitability.
There are many operational optimisations for the atmospheric tower that require no capital investment yet can still increase profitability. Optimisation of stripping steam flow rate, wash oil rate, pumparound rates, tower temperature, and heater operation can all impact distillate production. Several examples were presented, showing how profitability was improved at refineries with no capital investment.
Unit and tower simulation to evaluate the crude unit is the key to pointing out unit operational deficiencies and new opportunities, and to minimise risk. Understanding and evaluating operation can help minimise fouling, plugging and corrosion issues. Recommended modifications will be different for each refinery based on crude properties, existing equipment limits, and crude unit configuration. The authors have performed this analysis successfully at multiple refineries resulting in millions of dollars per year of increased profits.
Besides the atmospheric tower, a refiner should review crude slate selection as well as product specifications and blending pool contributions from each unit. A change to the crude slate can be made to accommodate existing equipment limitations.
As the world market becomes more distillate focused, refiners have plenty of options for low risk, zero capital investment modifications for maximised diesel production. The next article will cover maximising distillate yield with capital modifications.
Further Reading
- Annual Energy Outlook, Energy Information Administration (2010, 2013, 2014).
- Retail Diesel and Premium Gasoline Prices, Selected Countries (U.S. dollars per gallon, including and excluding taxes), Energy Information Administration, 19 Jun 2014.
- Engelhard Corporation, Maximizing Light Cycle Yield, The Catalyst Report.
- Barletta T, White S, Crude overhead system design considerations, PTQ, Q3 2007.
- Sandu C, Wright B, Innovative solutions for processing shale oils, Hydrocarbon Processing, Jul 2013.
The Authors
Joseph Musumeci is the founder of Ascent Engineering, Inc. (Houston, TX). Since 1997, he has been responsible for Ascent’s consulting and process design projects. He holds a BS in chemical engineering from Texas A&M University, and is a registered Professional Engineer in the state of Texas.
Steven W Stupin is a Technical Consultant and Senior Lead Process Engineer with Ascent Engineering, Inc. He has 26 years of refinery troubleshooting, revamp and design experience, and holds a BS in chemical engineering from the University of California Santa Barbara, and is a registered Professional Engineer in the state of California.
Stephanie Schlosser is a Process Engineer with Ascent Engineering, Inc. She has 10 years of process engineering experience and holds a BS in chemical engineering from the University of California at San Diego.
Thomas H Scholten is a Senior Lead Process Engineer with Ascent Engineering, Inc. He has 27 years of experience in refinery process design, chemicals process development, operations and site management. He holds a BS in chemical engineering from the University of Michigan and a PhD in chemical engineering from the University of Wisconsin-Madison.